In recent years, CNC machines have become increasingly popular among manufacturers. Thanks to their ability to increase efficiency and reduce waste when creating custom-built parts.
However, with so many types of CNC machines available, choosing the best unit for your shop isn’t that simple. It becomes more tedious if you don’t know the common differences between CNC mills and routers. One of the main reasons is that these machines perform the same functions.
Don’t worry though! In this blog, I’ll take you through all the notable features that set them apart. First, do you even know what a CNC machine is?
If your answer is No, let’s start from there!
Table of Contents
What is a CNC Machine?
For starters, CNC is an acronym for Computer Numerical Control. It’s a computer-controlled machine that runs off on design programs. These machines run off of CAM (Computer-Aided Manufacturing) and CAD (Computer-Aided Design). So, in essence, all CNC machines speak the same language and work on the same principle.
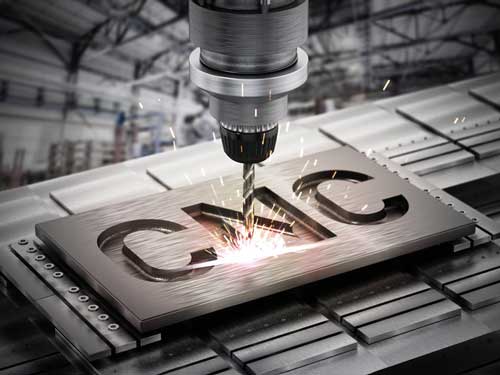
Moreover, they’re almost similar in terms of operation and functionality. For instance, they move a cutting tool across multiple axes when working on a workpiece. As a result, the tool cuts into the workpiece to create the desired shape. For this reason, you can use them.
Regardless of those similarities, these CNC-driven machines have certain noticeable differences.
Differences between a CNC Mill and Router
#1. Materials
The most significant difference between mills and routers is in the materials they’re designed to cut.
To start, a CNC router is less rigid and delivers less power to its cutting tool. However, that shouldn’t be an issue seeing that it’s designed to handle soft materials. For that, you can use it when working with materials like wood, foam, soft aluminum, and plastic.
On the contrary, a CNC milling machine is more robust than a router. This makes it ideal for handling tougher materials like titanium, steel, and cast iron. On the same note, a CNC mill can cut through thicker materials and with more varied shapes.
#2. Configuration
A CNC router features a spindle with 3 axes, that is; X, Y, and Z.
Another thing worth mentioning is that a CNC router is typically mounted on the set table. As a result, the spindle moves on the stationary table along the 3 axes. Moreover, a router has a shallow clearance since it’s designed to handle flatter materials.
Note, some types of CNC routers have more than 3 axes. Such machines are ideal for more complicated cutting. On the same note, they’re available in different shapes and sizes. This allows them to determine the final shape and appearance of the end product.
Like CNC routers, milling machines have 3 axes (X, Y & Z) as well. However, most mills don’t feature a stationary table. Instead, the spindle motor moves above the workpiece in a linear (X-Y) configuration. In addition, the Z-axis has a larger clearance, allowing the machine to make thicker cuts. Besides, milling machines use torque to make cuts instead of rotation speed.
#3. Machine Speed
The machine speed determines the rate at which your custom-built parts will be made. If you want to produce many copies of a part within a short time, a CNC router is the ideal machine for you. That’s because it operates quickly, thanks to the fast feed rate and high rpm spindle. In general, the spindle motor of a CNC router can range from 10,000 to 24,000 RPM.
CNC mills, on the other hand, have lower operational speeds than routers. Therefore, they take a bit longer to produce the same number of parts as routers. This is attributed to their slow cutting speeds and lower spindle rates, which can be as low as 1000rpm. Nonetheless, mills deliver higher torque and precision.
#4. Cutting Area
The cutting area of a CNC machine is considered the starting point of any project.
Generally speaking, CNC routers have a wider cutting coverage than mills. For that, routers are suitable for large cutting projects. For instance, you can use them to cut wide or large foam planks or wooden blocks. To be precise, most CNC routers have a work envelope of about 4 by 8 ft and 5 by 10 ft.
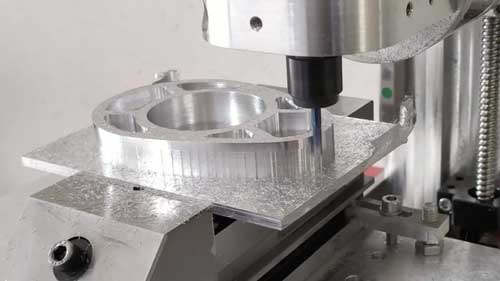
Remember, CNC machines, including mills, have different space options. So, although CNC mills have a smaller cutting area (400 by 500mm), you can find them in larger sizes as well. That aside, a CNC mill has a smaller worker envelope than a router. For that, it has more mass in a smaller area, making it more rigid.
Therefore, it’s suitable for handling a design that requires a lot of details. This rigidity and smaller envelope allow it to produce more accurate parts.
#5. Accuracy
Accuracy and precision are other important factors that set these CNC machines apart. In general, a CNC mill delivers much more accurate and precise cuts than routers. Due to this higher precision, they’re ideal for sensitive applications. Also, they’re suitable for applications in the medical, aerospace, and military industries.
Although CNC routers are computer-driven as well, they’ve lower precision mills. Instead, they’re intended for cutting soft materials. Also, they don’t use precise bits and mills. For that, mills are better suited for more complex shapes and cutting than routers.
#6. Cost
Apart from having distinguishing features, mills and routers vary in terms of price. For instance, the cost of buying a CNC router can range from $250 to $100,000. While the price of buying a milling machine ranges from $25,000 to $150,000.
Like any other machinery, the prices will be determined by factors like capabilities, speed, and size. All in all, CNC mills are more costly than routers of the same size.
#7. Industry Application
CNC routing and milling are commonly used in businesses and companies that need complex design. Surprisingly, most industries out there rely on these machines in one way or the other. Some of these industries are; military, automobile, electronics, medical, and oil & gas industries.
As you’ve seen though, each machine is suited for certain applications more than the other. As an example, routers are suitable for larger and less delicate products. While milling machines are ideal for delicate applications like cutting airplane components.
Moreover, CNC mills are better suited for industrial applications that involve heavy materials. But, routing is ideal for cutting soft materials when you want to make many copies within a short period.
Conclusion
Both routing and milling machines provide precise and consistent results than you would get manually. They offer other benefits like lower costs, versatility, lower maintenance, and better safety. However, you should always remember that these machines have very distinct purposes.
More importantly, they are designed to create and work with different materials. Thankfully, by understanding their differences, it’s quite simple to determine the ideal machine type for your project.
Up Next: Best lock miter router bit